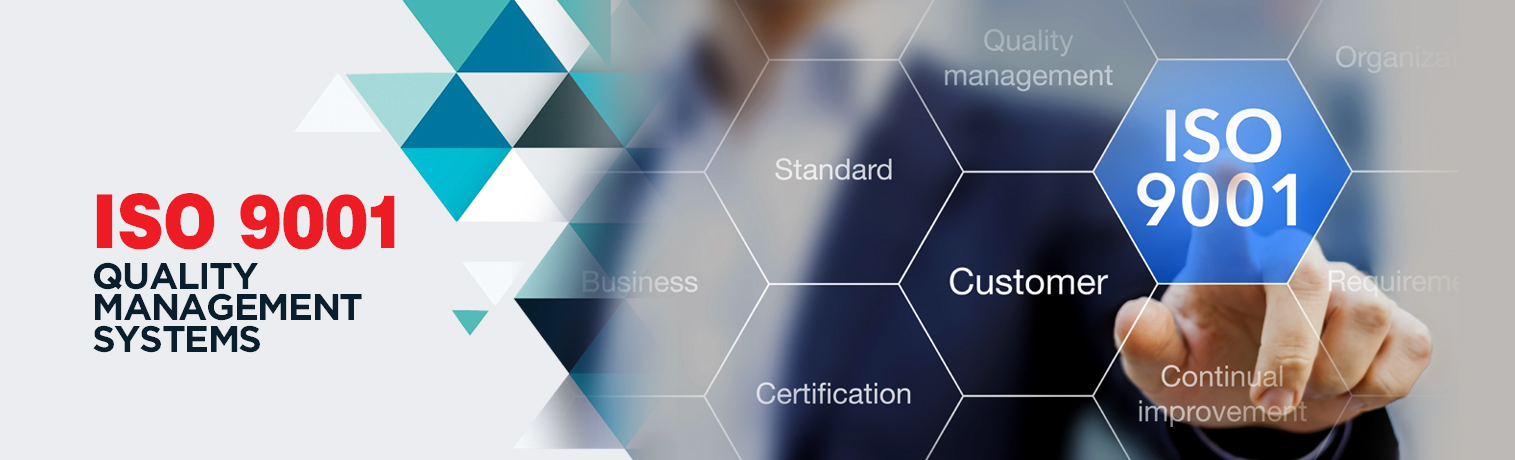
Would you aim to
Achieve the consistency of quality in your products & services and enhance your customer satisfaction?
-
- Work in a more efficient way as all your processes will be aligned and understood by everyone in the business or organization;
- Increase productivity and efficiency, bringing internal costs down;
- Meet the necessary statutory and regulatory requirements;
- Expand into new markets, as some sectors and clients require ISO 9001 before doing business;
- Identify and address the risks associated with your organization
Most organizations face challenges when developing a quality management system. These challenges are potentially greater due to:
- Availability of resources;
- Costs involved in setting up and maintaining a quality management system;
- Difficulty in understanding and applying a quality management system, especially concepts such as organizational context, organizational knowledge, process approach and risk-based thinking.
1. What is a quality management system?
A quality management system (QMS) is the way an organization directs and controls its activities that are related to achieving its intended results.
Broadly, it consists of organization’s structure together with the planning, processes, resources and documented information that is used to achieve quality objectives (such as for meeting customers’ and relevant interested parties’ requirements, to improve quality management system, or to improve products and services).
Every organization will already have a management structure and on that basis its quality management system is built. Organization might be fulfilling many of its requirements included in ISO 9001, but has simply not yet organized its activities into a formal quality management system.
2. Why have one?
The adoption of a QMS is a strategic decision that helps an organization to improve its overall performance and to provide a sound basis for its sustainable development initiatives.
Many organizations implement a formal quality management system after finding that their customers want assurance that the products and services they are looking to purchase or obtain will meet their requirements for quality. Those customers are looking for the confidence that can be provided by an organization offering products and services produced under an effective quality management system, such as one conforming to ISO 9001.
A quality management system, on its own, will not necessarily lead to an improvement of work processes or to improvements of products and services. It will not solve all industry problems. It is a means for organizations to take a more systematic approach to fulfilling the organization’s objectives, which in turn should achieve such improvements.
3. What is ISO 9001:2015
ISO 9001:2015 sets out the criteria for a quality management system and is the only standard in the family that can be certified to (although this is not a requirement).
4. This standard is applicable to:
Any legal dealing with sectors like, Pharma, Chemicals, Food Processing, Iron and Steel, Construction, Automotive, Aerospace, Granite, and Service organizations like Trading Houses, Banks, Hospitals, Diagnostic Centres, Insurance, Educational Institutions, Government Agencies, NGOs, etc. are eligible to implement and get certified.
Would you aim to
- Achieve the consistency of quality in your products & services and enhance your customer satisfaction?
- Demonstrate compliance with regulatory and legal requirements;
- Ensure the establishment of QMS practices that consistently yield safe and effective medical devices;
- Manage risk effectively;
- Improve processes and efficiencies as necessary;
- Gain a competitive advantage.
ISO 13485 -MEDIACL DEVICES QUALITY MANAGEMENT SYSTEM
1.Introduction to ISO 13485:2016-Medical devices- Quality management systems.
It should come as no surprise that, success in the medical devices industry means that you need to overcome compliance challenges. The case for quality compliance in the medical devices industry is indisputable – quality affects every stakeholder in the medical value chain. Quality is a fundamental concern at all stages of design, manufacturing, and marketing.
The cost of quality failure can be exorbitant as seen many times throughout history. Luckily, quality compliance today, though complex, is not as gargantuan of a task as it sounds.
2. What is a medical device?
A medical device is an instrument, apparatus, implement, machine, implant, in vitro reagent, or other similar article, that is intended for use in the diagnosis, prevention and treatment of disease or other medical conditions.
There is a huge variety of medical devices, ranging from basic hand tools to complex computer-controlled machines. These include simple devices like wound dressings and scalpels ; durable devices like wheelchairs and dentist chairs ; implantable devices like cardiac pacemakers and monitors, prosthetic limbs and prosthetic joints ; life-supporting devices like respirators and lung ventilators; sophisticated, software-controlled devices like CT scanners and MRI machines ; and in vitro diagnostic reagents and test kits.
3.What is ISO 13485:2016 -Medical Device Quality Management System:
A medical device quality management system (QMS) is a set of policies, processes and procedures that help an organization meet the requirements expected by its stakeholders. It is based on the Plan-Do-Check-Act cycle, a four-step management method used in business for the control and continual improvement of processes and products.
In the medical devices industry, a QMS is required by regulators in most countries. ISO 13485 enables an organization to consistently provide safe and effective medical devices and fulfil customer and regulatory requirements. It is also flexible enough to meet the individual needs of different types of medical devices organizations.
Regulations differ widely from one country to another. For this reason, ISO 13485 does not set detailed requirements, but asks a medical devices organization to identify those regulatory requirements that are relevant to its individual situation and incorporate them into its QMS.
4.Why to have ISO 13485:2016
- Eliminate uncertainty, and widen market opportunities;
- Increase access to more markets worldwide;
- Increase efficiency, cut costs and monitor supply chain performance;
- Produce safer and more effective medical devices meeting regulatory requirements and customer expectations.
5. Applicable to:
a) Medical Device Manufacturers and organizations involved in one or several stages of a Medical Device Lifecycle like Design and Development, Production, Storage, Distribution, Installation and Servicing.
b) External providers like Raw materials, Components, Sub-assemblies, Medical devices, Sterilization services, Calibration services, Distribution services and Maintenance services.
Would you like to
- Minimize business risks including regulatory risks and potential legal liabilities,
- Deliver products that consistently meet customer requirements, Get a listing in the Online Supplier Information System (OASIS) database,
- Greater consistency and traceability of products and services; Improvement of processes and operational efficiencies;
- Become a preferred supplier and gain customer and stakeholder trust;
- Continually improve and win more business in domestic and international markets.
AS 9100 D-AEROSPACE QUALITY MANAGEMENT SYSTEM
The risk of poor quality differs from industry to industry. If a part fails on a home appliance, in most cases it is likely a mere inconvenience to the customer. In contrast, if a part fails on a piece of equipment in the aviation, space or Défense industry the effect could potentially cause severe injury or loss of life. The importance of quality components within these industries cannot be overstated. To ensure adequate levels of quality and customer satisfaction in the aviation, space and Défense industries, the SAE AS9100 standard was developed. This standard defines the quality management system requirements to be used at all levels of the supply chain by suppliers from around the globe.
- What is AS9100D
AS 9100 is the international Quality Management System standard for the Aviation, Space and Défense (AS&D) industry, created by the IAQG, and AS9100 Rev D (2016) is the most recent version. The standard provides suppliers with requirements for creating and maintaining a comprehensive quality system for providing safe and reliable products to the ASD industry, as well as civil & military aviation requirements
The AS9100 includes not only the ISO 9001:2015 requirements, but also identifies additional requirements specifically for the aviation, space and Défense industries. Some of the changes to Revision D of the AS9100 standard include the addition of information regarding the handling of counterfeit parts, attention to the human factors of manufacturing quality, a focus on product safety, ethics training, and the process approach including SIPOC and PDCA tools, Risk Based Thinking, and monitoring supplier delivery performance.
- Why Implement AS 9100D
- To ensure Safety
- Airworthiness
- Product conformity and reliability
- Applicable to:
Manufacturing, Maintenance and service organizations across the aerospace/aviation sectors, including design, manufacturing, maintenance, and services providing companies.
Would like to
- Demonstrate ability to consistently provide products that meet customer and applicable statutory, regulatory and product safety requirements;
- Enhance customer satisfaction through the effective application of the system;
- Have repeat customers, increase customer loyalty, add new clients and increase business;
- Expand into new markets and Work in a more efficient way to increase productivity and efficiency, bringing internal costs down.
IATF 16949-AUTOMOTIVE QUALITY MANAGEMENT SYSTEM
One of the automotive industry’s most widely used international standards for quality management, ISO/TS 16949, is evolving with the publication of a new global industry standard by the International Automotive Task Force (IATF).
ISO/TS 16949, a technical specification for automotive sector quality management systems, has become one of the most widely used international standards in the automotive industry, harmonizing the different assessment and certification systems in the global automotive supply chain.
On October 3rd, 2016 IATF 16949:2016 was published by the IATF and supersedes and replaces the current ISO/TS 16949, defining the requirements of a quality management system for organizations in the automotive industry.
The primary focus of the IATF 16949 standard is the development of a Quality Management System that provides for continual improvement, emphasizing defect prevention and the reduction of variation and waste in the supply chain.
1.What is IATF 16949
The IATF 16949 standard provides guidance and tools for companies and organizations who want to ensure that their products consistently meet customer requirements and that quality and customer satisfaction are consistently improved. Requirements for certification to IATF 16949 are defined in the 2016 Revision 5 of the rules for achieving and maintaining IATF recognition.
2.Applicable to:
It can be used by any supplier, large or small, and should be applied throughout the automotive supply chain.
supplier providing design and development, production and, when relevant, assembly, installation and services of automotive related products, including products with embedded software.
Manufactures components, assemblies and parts for supply to the automotive industry.
Would like to
- Improve your reputation,
- Create new business connections,
- Gain competitive advantage,
- Increase laboratory effectiveness,
- Gain access to more contracts for testing and calibration,
- Offer proficiency on improving work processes,
- Offer more reliable and efficient lab testing and results & achieve customer reliability.
ISO 17025: LABORATORY QMS
National Accreditation Board for Testing and Calibration Laboratories (NABL) is a Constituent Board of Quality Council of India. NABL has been established with the objective to provide Government, Industry Associations and Industry in general with a scheme for third-party assessment of the quality and technical competence of testing and calibration laboratories.
In order to achieve this objective, NABL provides laboratory accreditation services to laboratories that are performing tests / calibrations in accordance with ISO/IEC 17025:2017 for testing laboratories.
1.What is ISO 17025: 2017- Laboratory Quality Management System
ISO/IEC 17025 is an international standard for testing and calibration laboratories. It was established with the aim of offering quality and improving the processes within laboratories. ISO/IEC 17025 has two key clauses; Management Requirements which are associated with the performance and efficiency of the Quality Management System inside the laboratory, and Technical Requirements which focus on the competencies of employees, testing methodology, equipment, and the test and calibration results.
2.Why ISO 17025: 2017-Laboratory Management System?
- Demonstrates your commitment to implement the requirements of this standard;
- Enable to become technically proficient and produce accurate test and calibration data;
- Able to increase your job opportunities because there are many large laboratory companies which will value your comprehensive knowledge as a professional in this field;
- Win contracts as certified professionals and laboratories, as the majority of customers prefer to receive services from certified labs;
- Enabling to maximize your earning potential.
3.Applicable to:
Testing Laboratories in the following disciplines: Chemical, Biological, Mechanical, Electrical, Electronics, Fluid Flow, Forensic, Non-Destructive (NDT), Photometry, Radiological, Diagnostic Radiology QA Testing, Software & IT System
Would you like to
- Improve Business Performance,
- Build Agile Resiliency and Scale,
- Increase Value of Benchmarking, Accelerate Adoption, Reduce rework,
- Improve product quality, Improve productivity and Average improvement in defect.
CMMI-CAPABILITY MATURITY MODEL INTEGRATION.
Originally created for the U.S. Department of Defense to assess the quality and capability of their software contractors, CMMI models have expanded beyond software engineering to help any organization in any industry build, improve, and measure their capabilities and improve performance.
For over 25 years, high-performing organizations around the world have achieved demonstrable, sustainable business results with CMMI.
Descriptive Practices Focused on Improvement
CMMI best practices focus on what needs to be done to improve performance and align operations to business goals. Designed to be understandable, accessible, flexible, and integrate with other methodologies such as agile, CMMI models help organizations understand their current level of capability and performance and offer a guide to optimize business results.
1. What is CMMI
The Capability Maturity Model Integration (CMMI) is a process and behavioral model that helps organizations streamline process improvement and encourage productive, efficient behaviors that decrease risks in software, product and service development.
The CMMI was developed by the Software Engineering Institute at Carnegie Mellon University as a process improvement tool for projects, divisions or organizations.
The CMMI starts with an appraisal process that evaluates three specific areas: process and service development, service establishment and management, and product and service acquisition. It’s designed to help improve performance by providing businesses with everything they need to consistently develop better products and services.
- CMMI Maturity Levels
The CMMI model breaks down organizational maturity into five levels. For businesses that embrace CMMI, the goal is to raise the organization up to Level 5, the “optimizing” maturity level. Once businesses reach this level, they aren’t done with the CMMI. Instead, they focus on maintenance and regular improvements.
3.0 CMMI DEV 2.0
For 25+ years, high-performing organizations have achieved clear, sustainable business results with ISACA’s CMMI maturity models. Originally created for the U.S. Department of Defense to assess the quality and capability of their software contractors, ISACA’s CMMI models have expanded beyond software engineering to help organizations around the world, in any industry, understand their current level of capability and performance and offer a guide to optimize business results.
Integrated CMMI product suite provides best practices that enable organizations to improve performance of their key capabilities, providing a clear roadmap for building, improving, and benchmarking capability.
This is a model with customized set of parameters for companies in the IT sector. The guidelines apply to different business environments, with the focus on enabling organizations meet their defined performance improvement needs.
CMMI V2.0 supports companies to identify their existing level of capability in a timely manner. This helps an organization mark the areas of improvement and identify the need for efficient use of resources.
CMMI V2.0 helps organizations quickly understand their current level of capability and performance in the context of their own business objectives and compared to similar organizations.
CMMI V2.0 is a dynamic model with the ability to be updated quickly to include proven new methodologies and practices. By focusing more on meaningful outcomes and linking improvements with organizations’ key business goals, V2.0 provides value to organizations that extends well beyond appraisals and maturity ratings
- Features and Benefits
- Applicability
- Consulting Methodology
- CMMI is applicable to
CMMI has been adopted by government organizations and across many industries (e.g., software, finance, manufacturing, services).