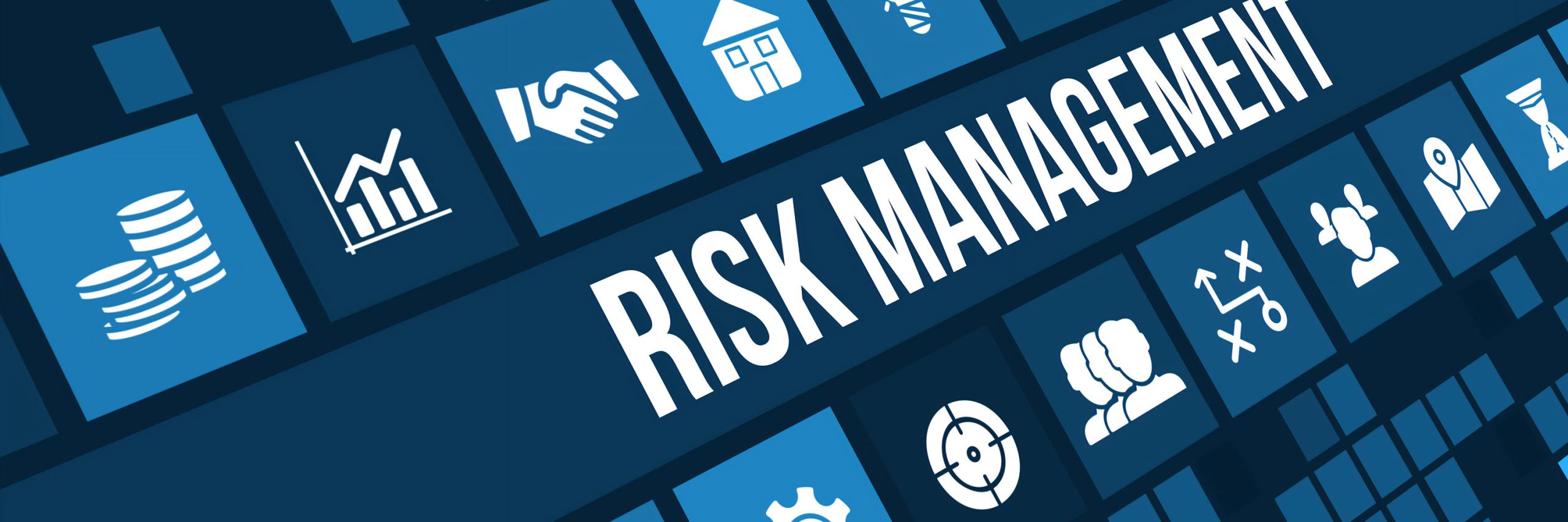
1) SAFETY AND LIFE SAVING SERVICES
- Workplace Safety: Building a strong workplace
- Ergonomics Safety Audit: Enhancing workplace health and Productivity
- Hospital Safety Audit: Ensuring Patient and Staff Safety
- Residential And High-Rise Building Safety Audit: Ensuring Resident Well-Being and Structural Integrity
- Hotel Safety Audit: Ensuring Guest and Staff Safety
- School Safety Audit: Creating A Safe Learning Environment
- Commercial Building Safety Audit: Ensuring Workplace Safety and Regulatory Compliance
- Working At Heights Safety Audit: Ensuring Safe Practices and Compliance
- Construction Safety Audit: Ensuring A Safe and Compliant Worksite
- Behavior-Based Safety (BBS) Audit
- Psychological Assessments in Workplace Safety
2) CONTRCATOR SAFETY MANAGEMENT.
3) FIRE SAFETY AUDIT.
4) ELECTRICAL SAFETY AND AUDIT: ENSURING RISK-FREE WORK ENVIRONMENTS
- INDUSTRIAL HYGIENE AUDIT: SAFEGUARDING HEALTH IN THE WORKPLACE
6) SAFETY CULTURE TRANSFORMATION
7) SAFETY PROFESSIONALS PLACEMENT SERVICES
Would you be interested to proactively address safety challenges to protect your work force, reduce incidents, and create a safer, more productive work environment with the below commitments?
- Comply with industry regulations and conduct frequent safety audits?
- Improve ergonomics and workplace design for better employee well-being?
Promote a culture of safety by encouraging reporting of hazards and near-misses? - Maintain and inspect equipment regularly to prevent malfunctions?
- Provide proper PPE and ensure it is used correctly.
Monitor employees’ mental health and provide resources for stress management.
Enhance emergency preparedness with clear evacuation plans and accessible fire safety equipment.
Safety is a fundamental concern in every industry, from manufacturing and healthcare to information security and supply chain management. Ensuring a safe environment for workers, consumers, and organizations is crucial for sustainability, regulatory compliance, and operational efficiency. However, achieving high safety standards comes with various challenges that require proactive solutions.
SAFETY SERVICES
- WORKPLACE SAFETY: BUILDING A STRONG WORK PLACE
Workplace safety is a multidisciplinary approach to protecting employees’ health, preventing injuries, and reducing risks in the work environment. A strong workplace safety program is critical for compliance, operational efficiency, and employee well-being.
Benefits of a Strong Workplace Safety Program
- Reduces incidents and injuries, improving employee well-being.
- Boosts productivity by minimizing downtime.
- Enhances compliance with regulatory standards.
- Improves employee morale and engagement.
- Reduces insurance premiums and liability costs.
- ERGONOMICS SAFETY AUDIT: ENHANCING WORKPLACE HEALTH AND PRODUCTIVITY
An ergonomics audit is a comprehensive evaluation of workplace design, tools, and practices to ensure they align with ergonomic principles. The goal is to reduce the risk of musculoskeletal disorders (MSDs), improve employee comfort, and boost productivity by optimizing the interaction between people and their work environment.
Common Ergonomic Issues Identified in Audits
- Poor sitting posture due to non-adjustable chairs or incorrect desk height.
- Prolonged standing without proper anti-fatigue measures.
- Repetitive strain from manual handling tasks.
- Inadequate lighting causing strain and awkward postures.
- Use of non-ergonomic tools leading to hand and wrist injuries
- HOSPITAL SAFETY AUDIT: ENSURING PATIENT AND STAFF SAFETY
A hospital safety audit is a comprehensive assessment of hospital facilities, operations, and safety practices to ensure a safe environment for patients, staff, and visitors. It covers physical safety, clinical processes, infection control, fire safety, and emergency preparedness, helping hospitals comply with healthcare standards and regulations.
Benefits of a Hospital Safety Audit
- Reduces patient and staff risks.
- Ensures compliance with regulatory standards (NABH, JCI, ISO 45001).
- Improves infection control and clinical outcomes.
- Enhances patient trust and hospital reputation.
- Promotes a culture of safety and continuous improvement.
- RESIDENTIAL AND HIGH-RISE BUILDING SAFETY AUDIT: ENSURING RESIDENT WELL-BEING AND STRUCTURAL INTEGRITY
A residential and high-rise building safety audit is a thorough assessment aimed at identifying safety risks, ensuring compliance with regulations, and protecting residents from hazards. This audit covers structural safety, fire safety, electrical systems, emergency preparedness, and overall building security.
Objectives of a Residential and High-Rise Building Safety Audit
- Ensure compliance with local building and fire safety codes.
- Identify and mitigate risks to residents and visitors.
- Improve emergency response and evacuation preparedness.
- Enhance the safety and security of common areas.
- Promote sustainable and safe living conditions.
- HOTEL SAFETY AUDIT: ENSURING GUEST AND STAFF SAFETY
A hotel safety audit is a systematic assessment of hotel operations, facilities, and processes to identify potential risks and ensure the safety of guests, staff, and property. It covers fire safety, security, health and hygiene, emergency preparedness, and more, ensuring compliance with local regulations and international standards.
Benefits of a Hotel Safety Audit
- Protects guests, staff, and property from hazards.
- Ensures compliance with legal and regulatory requirements.
- Enhances hotel reputation and guest trust.
- Reduces liability risks and insurance premiums.
- Promotes a proactive safety culture.
- SCHOOL SAFETY AUDIT: CREATING A SAFE LEARNING ENVIRONMENT
A school safety audit is a thorough evaluation of a school’s physical environment, safety policies, and emergency procedures to ensure the well-being of students, staff, and visitors. It covers multiple aspects of safety, including physical security, health, emergency preparedness, and psychosocial factors.
Benefits of a School Safety Audit
- Reduces risks and protects students, staff, and visitors.
- Builds trust among parents and the community.
- Ensures compliance with regulatory standards.
- Creates a supportive environment for learning and development.
- Promotes a culture of safety and well-being.
- COMMERCIAL BUILDING SAFETY AUDIT: ENSURING WORKPLACE SAFETY AND REGULATORY COMPLIANCE
A commercial building safety audit is a comprehensive evaluation of a building’s infrastructure, operations, and safety systems to ensure the safety of occupants, assets, and visitors. It helps identify risks, ensure compliance with legal requirements, and promote a safe and efficient working environment.
Benefits of a Commercial Building Safety Audit
- Protects occupants and assets from risks.
- Ensures compliance with regulatory requirements.
- Reduces liabilities and insurance costs.
- Enhances operational efficiency and safety culture.
- Promotes a healthy and secure work environment.
- WORKING AT HEIGHTS SAFETY AUDIT: ENSURING SAFE PRACTICES AND COMPLIANCE
A Working at Heights Safety Audit assesses and verifies the safety measures, processes, and controls in place for workers operating at elevated levels. The audit ensures compliance with relevant safety standards and minimizes risks associated with working at heights. Falls from height remain one of the leading causes of workplace injuries and fatalities, making these audits essential for protecting workers and maintaining a safe environment.
Benefits of a Working at Heights Safety Audit
- Reduces workplace injuries and fatalities.
- Ensures compliance with safety regulations.
- Boosts worker confidence and productivity.
- Minimizes downtime and liability risks.
- Promotes a proactive safety culture
- CONSTRUCTION SAFETY AUDIT: ENSURING A SAFE AND COMPLIANT WORKSITE
A construction safety audit is a critical evaluation of a construction site to identify potential safety hazards, ensure compliance with legal and industry standards, and protect workers from risks. It focuses on assessing site conditions, equipment, processes, and overall safety management practices.
Benefits of a Construction Safety Audit
- Reduces accidents, injuries, and fatalities.
- Improves worker morale and productivity.
- Ensures compliance with regulations and standards.
- Minimizes project delays and liability risks.
- Enhances the overall safety culture on-site.
- SCAFFOLDING SAFETY: KEY GUIDELINES FOR A SAFE WORK ENVIRONMENT
Scaffolding safety is critical on construction sites to protect workers from falls, injuries, and potential fatalities. Proper planning, setup, and regular inspection of scaffolding systems are essential to prevent accidents. Scaffolding hazards mainly include falls, collapsing structures, and falling objects.
Scaffolding Safety Benefits
- Reduces the risk of accidents and injuries.
- Ensures compliance with legal and safety standards.
- Improves worker confidence and productivity.
- Minimizes project delays and associated costs.
- BEHAVIOR-BASED SAFETY (BBS) AUDIT
A BBS Audit evaluates the implementation, effectiveness, and sustainability of a Behavior-Based Safety program. It focuses on verifying that observations, feedback processes, and data-driven improvements are conducted effectively and aligned with the organization’s safety goals.
Benefits of BBS Audits
- Ensures the integrity and effectiveness of the BBS program
- Identifies behavioral trends and risk areas
- Improves employee engagement and trust in the process
- Promotes data-driven decision-making
- Supports continuous improvement and long-term safety performance
- PSYCHOLOGICAL ASSESSMENTS IN WORKPLACE SAFETY
Psychological assessments are tools used to evaluate an individual’s mental health, cognitive abilities, personality traits, emotional resilience, and stress response—critical factors that influence workplace safety and performance. These assessments help identify risks related to human behavior and mental well-being, contributing to proactive safety management.
Key Objectives of Psychological Assessments
- Assess mental readiness and emotional stability for high-risk tasks
- Identify cognitive and behavioral patterns that may lead to unsafe behaviors
- Evaluate stress management and resilience in crisis situations
- Support employee well-being and mental health initiatives
- Enhance safety culture by addressing psychological factors
- CONTRACTOR SAFETY MANAGEMENT (CSM)
Contractor Safety Management is a structured process to ensure that contractors and subcontractors meet an organization’s health, safety, and environmental (HSE) standards. Since contractors often perform high-risk tasks, managing their safety is critical to reducing workplace incidents and ensuring compliance with legal and regulatory requirements.
Objectives of Contractor Safety Management
- Ensure contractors comply with safety standards and legal requirements.
- Reduce workplace incidents and risks associated with contractor activities.
- Align contractor safety practices with the organization’s safety culture.
- Enhance monitoring, evaluation, and continuous improvement of contractor performance.
Key Steps in Contractor Safety Management
- Pre-Qualification and Selection
- Evaluate contractors’ safety performance history and competency.
- Require documentation of safety programs, training records, and certifications.
- Use a contractor pre-qualification questionnaire (focus on accident history, regulatory compliance, and HSE policies).
- Contractor Induction and Training
- Provide safety induction before starting work.
- Cover site-specific hazards, emergency procedures, PPE requirements, and safe work practices.
- Ensure job-specific training for high-risk tasks (e.g., working at heights, confined spaces).
- Risk Assessment and Safe Work Planning
- Conduct joint risk assessments with contractors.
- Develop Job Hazard Analysis (JHA) or Safe Work Method Statements (SWMS) for high-risk activities.
- Ensure control measures are in place for identified hazards.
- Monitoring and Supervision
- Assign safety supervisors to oversee contractor activities.
- Conduct regular site inspections and audits to ensure compliance.
- Use observation checklists to track adherence to safety procedures.
- Incident Reporting and Investigation
- Require contractors to report incidents and near-misses immediately.
- Conduct joint incident investigations to identify root causes and corrective actions.
- Share lessons learned with all contractors to prevent recurrence.
- Performance Evaluation and Continuous Improvement
- Track contractor safety performance with KPIs (e.g., total recordable incident rate, lost time injury frequency rate).
- Conduct regular performance reviews and feedback sessions.
- Reward contractors with strong safety records and improvement initiatives.
Benefits of Contractor Safety Management
- Improves Overall Safety Performance: Reduces risks from third-party activities.
- Ensures Regulatory Compliance: Meets legal and industry standards.
- Protects Business Reputation: Minimizes the risk of incidents involving external personnel.
- Enhances Collaboration: Encourages contractors to adopt a proactive safety approach.
Contractor Safety Audit
A Contractor Safety Audit is a structured evaluation to ensure contractors comply with the organization’s safety standards, legal regulations, and best practices. It focuses on identifying gaps, assessing risks, and improving contractor safety performance.
Objectives of a Contractor Safety Audit
- Verify contractor compliance with safety policies and procedures.
- Identify hazards and unsafe practices in contractor activities.
- Assess the effectiveness of contractor safety management systems.
- Ensure proper risk mitigation measures are in place.
- Drive continuous improvement in contractor safety performance.
Benefits of Implementing Contractor Safety Requirements
- Reduces workplace incidents and injuries.
- Ensures legal and regulatory compliance.
- Protects the organization’s reputation.
- Improves contractor productivity and performance.
- Fosters a positive safety culture across the organization.
- FIRE SAFETY AUDIT: ENSURING COMPREHENSIVE FIRE RISK MANAGEMENT
A Fire Safety Audit is a structured evaluation of fire hazards in a facility to ensure compliance with safety standards and reduce the risk of fire incidents. It focuses on identifying gaps in fire prevention, protection, and response measures, offering actionable recommendations to improve safety. Fire safety audits are essential for industries such as manufacturing, oil & gas, chemical plants, hospitals, schools, hotels, and high-rise buildings.
Key Benefits of Fire Safety Audit
- Early Risk Detection: Prevent potential fire incidents.
- Compliance: Ensure adherence to fire safety regulations.
- Enhanced Emergency Preparedness: Improve response times and minimize impact.
- Cost Savings: Reduce insurance premiums and prevent costly fire damage.
- Increased Employee Confidence: Create a safer working environment.
Who Needs a Fire Safety Audit?
- Manufacturing Plants
- Chemical and Petrochemical Facilities
- Warehouses and Storage Units
- Hospitals and Healthcare Centers
- Educational Institutions
- Commercial and Residential High-Rise Buildings
- Hotels and Hospitality Sector
Fire Audit: Comprehensive Fire Risk Assessment and Safety Compliance
A Fire Audit is a thorough evaluation of fire safety measures in a facility. It aims to assess fire hazards, ensure regulatory compliance, and improve fire prevention, protection, and emergency response systems. Fire audits are essential for safeguarding human lives, protecting assets, and minimizing business disruptions.
Benefits of a Fire Audit
- Early Detection of Hazards: Prevent fire incidents.
- Regulatory Compliance: Avoid penalties and legal issues.
- Improved Emergency Preparedness: Reduce response time and ensure safe evacuation.
- Enhanced Safety Culture: Increase fire safety awareness among employees.
- Cost Savings: Lower insurance premiums and avoid costly damages.
Industries Requiring Fire Audits
- Manufacturing and Processing Plants
- Oil & Gas Facilities
- Chemical Industries
- Warehouses and Logistics Centers
- Healthcare Institutions
- Educational Facilities
- Hospitality and High-Rise Buildings
4.ELECTRICAL SAFETY AND AUDIT: ENSURING RISK-FREE WORK ENVIRONMENTS
An electrical safety audit (ESA) is a comprehensive evaluation of an organization’s electrical systems and practices to identify hazards, ensure regulatory compliance, and promote safe working conditions. Electrical incidents can cause serious injuries, fires, equipment damage, and business disruptions, making these audits critical for workplace safety.
Common Hazards Found in Electrical Safety Audits
- Improper grounding and earthing systems.
- Overloaded circuits and use of unauthorized extensions.
- Poorly maintained or outdated electrical panels.
- Unprotected live parts and exposed wires.
- Lack of arc flash protection measures.
Benefits of Electrical Safety Audits
- Reduces electrical hazards and ensures a safer workplace.
- Prevents equipment failures and costly downtime.
- Ensures compliance with safety regulations.
- Improves energy efficiency and system reliability.
- Reduces insurance costs and liability risks.
Electrical Residual Life Assessment (RLA): Extending Equipment Lifespan and Ensuring Reliability
Electrical Residual Life Assessment (RLA) is a process used to determine the remaining useful life of electrical equipment and systems. This assessment helps identify aging-related issues, predict potential failures, and recommend actions for life extension or replacement. It is crucial for industries relying on continuous operations, such as power plants, manufacturing, oil & gas, and data centers.
Key Equipment Covered in Electrical RLA
- Transformers
- Motors and Generators
- Switchgears and Circuit Breakers
- Cables and Busbars
- Relays and Protection Systems
- Power Electronics (VFDs, UPS systems, etc.)
Benefits of Electrical Residual Life Assessment
- Failure Prevention: Identify potential failures before they occur.
- Cost Savings: Reduce unplanned maintenance and extend equipment life.
- Improved Reliability: Enhance system performance and reduce downtime.
- Optimized Capital Planning: Make informed decisions about equipment replacement and upgrades.
- Compliance: Meet regulatory and industry standards.
Thermography Assessments: Comprehensive Heat Mapping for Preventive Maintenance
A thermography assessment involves using infrared technology to detect temperature anomalies in electrical, mechanical, and structural systems. It’s an effective non-contact diagnostic method that provides insights into the condition of equipment, helping identify potential failures, reduce energy losses, and improve overall safety and reliability.
Applications of Thermography Assessments
- Electrical Systems
- Detect overheating in switchboards, circuit breakers, and control panels.
- Identify loose connections, overloaded circuits, and imbalanced loads.
- Spot insulation failures in cables and transformers.
- Mechanical Systems
- Assess temperature patterns in bearings, motors, and rotating equipment.
- Detect misalignment, lubrication issues, and excessive friction.
- Monitor HVAC systems (compressors, pumps, fans).
- Structural Assessments
- Identify heat loss in building insulation.
- Detect moisture intrusion and water leaks in roofs and walls.
- Assess fire hazards in storage areas.
- Process Industries
- Monitor temperature-sensitive processes.
- Ensure uniform heating in kilns, furnaces, and reactors.
- Detect leaks in steam and hot water systems.
Key Benefits of Thermography Assessments
- Early Fault Detection: Avoid costly breakdowns and unplanned downtime.
- Increased Safety: Reduce risks of electrical fires, equipment failures, and overheating.
- Energy Savings: Improve energy efficiency by detecting heat losses.
- Non-Intrusive: No need for system shutdowns during assessments.
- Compliance Support: Meet safety, insurance, and regulatory requirements.
Arc Flash Assessments: Protecting Personnel from Electrical Hazards
An Arc Flash Assessment evaluates the potential risks of arc flash incidents in electrical systems and helps implement measures to protect workers from severe injuries caused by these high-energy events. This assessment is critical for industries where electrical work is part of daily operations, such as manufacturing, power plants, oil & gas, and commercial buildings.
What is an Arc Flash?
An arc flash is an electrical explosion caused by a fault or short circuit in energized electrical equipment. It results in:
- Extreme heat (up to 35,000°F or 19,400°C)
- Blast pressure causing equipment damage and serious injury
- Molten metal and shrapnel ejected at high speed
- Intense light and sound
Key Benefits of Arc Flash Assessments
- Enhanced Worker Safety: Reduce the risk of serious injuries and fatalities.
- Compliance: Ensure adherence to safety standards and regulatory requirements.
- Improved Equipment Reliability: Minimize equipment damage and operational disruptions.
- Informed Decision-Making: Optimize maintenance and capital planning.
- Reduced Insurance Costs and Liability Risks.
- INDUSTRIAL HYGIENE AUDIT: SAFEGUARDING HEALTH IN THE WORKPLACE
An industrial hygiene audit is a comprehensive assessment of workplace environments to identify, evaluate, and control hazards that could affect employees’ health. It focuses on anticipating, recognizing, evaluating, and controlling occupational health risks related to physical, chemical, biological, and ergonomic factors.
Benefits of an Industrial Hygiene Audit
- Reduces health risks and prevents occupational illnesses.
- Enhances regulatory compliance and avoids penalties.
- Improves employee health, morale, and productivity.
- Reduces absenteeism and healthcare costs.
- Supports a proactive approach to workplace health management.
6) SAFETY CULTURE TRANSFORMATION
Safety Culture Transformation Process
A strong safety culture is essential for reducing incidents, improving operational efficiency, and achieving long-term success. Transforming safety culture requires a structured approach that involves leadership commitment, employee engagement, continuous learning, and behavioral changes.
- Assessment and Diagnosis
The transformation begins with a comprehensive assessment of the current safety culture.
- Leadership Commitment and Vision
Leadership plays a critical role in driving cultural change. Leaders must actively promote safety as a core organizational value.
- Building Engagement and Ownership
Employees should be involved in safety improvements and empowered to take ownership.
- Training and Competence Development
Transforming safety culture requires ongoing education and skill-building.
- Integrating Safety into Business Processes
Safety should be an integral part of operational and decision-making processes.
- Reinforcing Desired Behaviours
Encourage continuous improvement by reinforcing safe behaviors and addressing unsafe ones.
- Continuous Improvement and Sustainability
A safety culture transformation is a long-term process that requires sustained effort.
Safety Culture Maturity Stages
Organizations typically progress through these stages:
- Pathological – Safety is ignored or seen as a burden.
- Reactive – Safety improvements occur only after incidents.
- Calculative – Systems and processes are in place but not deeply embedded.
- Proactive – Safety is actively managed and continuously improved.
- Generative – Safety is a core value, and everyone takes responsibility for it.
Challenges in Safety Culture Transformation
- Resistance to change and complacency
- Lack of leadership commitment
- Inadequate communication and training
- Insufficient resources for safety initiatives
- Failure to measure and monitor cultural change
Success Factors
- Strong leadership and visible commitment
- Employee engagement at all levels
- Effective communication and feedback loops
- Integration of safety into core business processes
- Continuous improvement through monitoring and adaptation
Safety Perception Survey (SPS)
A Safety Perception Survey is a tool designed to gauge employees’ perceptions, attitudes, and beliefs regarding the safety culture within an organization. It helps identify gaps between management’s intentions and employees’ actual experiences related to workplace safety.
Why Conduct a Safety Perception Survey?
- Assess the current state of the safety culture
- Identify strengths and areas for improvement
- Promote employee engagement in safety initiatives
- Provide a baseline for measuring progress over time
- Benchmark results against industry standards
Behavior-Based Safety (BBS) is a proactive process that focuses on identifying and modifying unsafe behaviors in the workplace to prevent incidents and injuries. It emphasizes observing employees’ behavior, providing constructive feedback, and reinforcing safe practices.
Core Principles of BBS
- Focus on Behavior: Human behavior is the leading cause of workplace incidents.
- Employee Involvement: Employees are key in observing and correcting behavior.
- Positive Reinforcement: Encourage safe behavior rather than punishing unsafe practices.
- Data-Driven Process: Use observation data to identify trends and improve safety programs.
- Continuous Improvement: Regular feedback and reviews help sustain long-term change.
Benefits of Behavior-Based Safety
- Reduced Incidents and Injuries: Focuses on preventing at-risk behaviors.
- Improved Safety Culture: Encourages openness and shared responsibility.
- Higher Employee Engagement: Involves employees in safety processes.
- Data-Driven Decisions: Provides actionable insights from observation data.
- Sustained Long-Term Improvement: Encourages continuous growth and learning.
Safety Performance Leadership Survey
A Safety Performance Leadership Survey assesses how leadership attitudes, actions, and behaviors influence the organization’s safety culture and performance. This survey helps identify gaps, set improvement goals, and engage leadership in driving a safer workplace.
Purpose of the Survey
- Evaluate leaders’ commitment to safety.
- Measure perceptions of leadership’s influence on safety performance.
- Identify areas for improvement in safety leadership practices.
- Enhance accountability and engagement at all leadership levels.
Change Management in Safety and Organizational Processes
Change management is a structured approach to transitioning individuals, teams, and organizations from a current state to a desired future state. In safety and operational environments, managing change effectively ensures that safety risks are minimized, employees are engaged, and improvements are sustainable.
Objectives of Change Management
- Ensure the safety and well-being of employees during transitions.
- Minimize resistance and disruptions.
- Engage stakeholders to drive successful implementation.
- Identify and mitigate risks associated with changes.
- Build a resilient and adaptable organizational culture.
Types of Change in Safety and Operations
- Organizational Change – Restructuring, mergers, or leadership transitions.
- Process Change – New procedures, production methods, or standards.
- Technological Change – Implementation of new equipment or systems.
- Regulatory Change – Compliance with updated legal and safety standards.
- Cultural Change – Building a stronger safety culture or behavioral transformation.
Common Challenges in Change Management
- Resistance to Change: Fear of the unknown or loss of control.
- Poor Communication: Lack of clarity can lead to confusion and frustration.
- Insufficient Resources: Inadequate training, time, or tools can hinder success.
- Leadership Misalignment: Inconsistent leadership behaviors can undermine the process.
- Cultural Barriers: Deep-rooted organizational norms may resist change.
- SAFETY PROFESSIONALS PLACEMENT SERVICES
Safety professionals play a critical role in ensuring workplace safety, compliance, and risk mitigation. Many organizations rely on safety professionals placement services to recruit qualified safety officers, managers, and consultants who can help maintain regulatory compliance and create a safe work environment. However, the recruitment and placement of safety professionals come with unique challenges.
Safety professional’s placement services specialize in sourcing and hiring qualified experts for various industries, including:
- Construction & Engineering (Safety Officers, Site Safety Managers)
- Manufacturing & Industrial (Health & Safety Managers, Compliance Auditors)
- Oil & Gas, Energy, and Utilities (HSE Advisors, Risk Analysts)
- Healthcare & Pharmaceuticals (Infection Control Officers, Biosafety Experts)
- Supply Chain & Logistics (Transportation Safety Managers, Compliance Coordinators)
- Cybersecurity & Information Safety (Virtual CISOs, Security Compliance Experts)
Types of Placement Services
- Permanent Staffing – Recruiting full-time, long-term safety professionals.
- Contract & Temporary Staffing – Providing short-term or project-based professionals.
- Consulting & Advisory Services – Deploying experts to assess, audit, and develop safety programs.
- Virtual Safety Officers – Remote safety professionals who provide guidance and compliance monitoring.
- ISO 45001:2018-OCCUPATIONAL HEALTH AND SAFETY MANAGEMENT SYSTEM
Would you like Reduction of workplace incidents, reduced absenteeism and staff turnover, leading to increased productivity, reduced cost of insurance premiums, creation of a health and safety culture, whereby employees are encouraged to take an active role in their own OH&S, Reinforced leadership commitment to proactively improve OH&S performance, Ability to meet legal and regulatory requirements, Enhanced reputation and Improved staff morale.
ISO 45001:2018-OCCUPATIONAL HEALTH AND SAFETY MANAGEMENT SYSTEM. |
Health and safety in the workplace are the number one concern of most businesses, yet still deaths and injuries occur. ISO 45001 sets the minimum standard of practice to protect employees worldwide.
According to the International Labour Organization (ILO), there are currently more than 2.78 million deaths a year as a result of occupational accidents or work-related diseases, in addition to 374 million non-fatal injuries and illnesses. Aside from the enormous impact on families and communities, the cost to business and economies is significant.
1.What is ISO 45001?
ISO 45001, Occupational health and safety management systems – Requirements with guidance for use, is the world’s first International Standard for occupational health and safety (OH&S). It provides a framework to increase safety, reduce workplace risks and enhance health and well-being at work, enabling an organization to proactively improve its OH&S performance.
2.Why Implement ISO 45001?
- Makes a safe place to work.
- reduced number of incidents,
- employee absentee
1) SAFETY AND LIFE SAVING SERVICES
- Workplace Safety: Building a strong workplace
- Ergonomics Safety Audit: Enhancing workplace health and Productivity
- Hospital Safety Audit: Ensuring Patient and Staff Safety
- Residential And High-Rise Building Safety Audit: Ensuring Resident Well-Being and Structural Integrity
- Hotel Safety Audit: Ensuring Guest and Staff Safety
- School Safety Audit: Creating A Safe Learning Environment
- Commercial Building Safety Audit: Ensuring Workplace Safety and Regulatory Compliance
- Working At Heights Safety Audit: Ensuring Safe Practices and Compliance
- Construction Safety Audit: Ensuring A Safe and Compliant Worksite
- Behavior-Based Safety (BBS) Audit
- Psychological Assessments in Workplace Safety
2) CONTRCATOR SAFETY MANAGEMENT.
3) FIRE SAFETY AUDIT.
4) ELECTRICAL SAFETY AND AUDIT: ENSURING RISK-FREE WORK ENVIRONMENTS
- INDUSTRIAL HYGIENE AUDIT: SAFEGUARDING HEALTH IN THE WORKPLACE
6) SAFETY CULTURE TRANSFORMATION
7) SAFETY PROFESSIONALS PLACEMENT SERVICES
Would you be interested to proactively address safety challenges to protect your work force, reduce incidents, and create a safer, more productive work environment with the below commitments?
- Comply with industry regulations and conduct frequent safety audits?
- Improve ergonomics and workplace design for better employee well-being?
Promote a culture of safety by encouraging reporting of hazards and near-misses? - Maintain and inspect equipment regularly to prevent malfunctions?
- Provide proper PPE and ensure it is used correctly.
Monitor employees’ mental health and provide resources for stress management.
Enhance emergency preparedness with clear evacuation plans and accessible fire safety equipment.
Safety is a fundamental concern in every industry, from manufacturing and healthcare to information security and supply chain management. Ensuring a safe environment for workers, consumers, and organizations is crucial for sustainability, regulatory compliance, and operational efficiency. However, achieving high safety standards comes with various challenges that require proactive solutions.
SAFETY SERVICES
- WORKPLACE SAFETY: BUILDING A STRONG WORK PLACE
Workplace safety is a multidisciplinary approach to protecting employees’ health, preventing injuries, and reducing risks in the work environment. A strong workplace safety program is critical for compliance, operational efficiency, and employee well-being.
Benefits of a Strong Workplace Safety Program
- Reduces incidents and injuries, improving employee well-being.
- Boosts productivity by minimizing downtime.
- Enhances compliance with regulatory standards.
- Improves employee morale and engagement.
- Reduces insurance premiums and liability costs.
- ERGONOMICS SAFETY AUDIT: ENHANCING WORKPLACE HEALTH AND PRODUCTIVITY
An ergonomics audit is a comprehensive evaluation of workplace design, tools, and practices to ensure they align with ergonomic principles. The goal is to reduce the risk of musculoskeletal disorders (MSDs), improve employee comfort, and boost productivity by optimizing the interaction between people and their work environment.
Common Ergonomic Issues Identified in Audits
- Poor sitting posture due to non-adjustable chairs or incorrect desk height.
- Prolonged standing without proper anti-fatigue measures.
- Repetitive strain from manual handling tasks.
- Inadequate lighting causing strain and awkward postures.
- Use of non-ergonomic tools leading to hand and wrist injuries.
- HOSPITAL SAFETY AUDIT: ENSURING PATIENT AND STAFF SAFETY
A hospital safety audit is a comprehensive assessment of hospital facilities, operations, and safety practices to ensure a safe environment for patients, staff, and visitors. It covers physical safety, clinical processes, infection control, fire safety, and emergency preparedness, helping hospitals comply with healthcare standards and regulations.
Benefits of a Hospital Safety Audit
- Reduces patient and staff risks.
- Ensures compliance with regulatory standards (NABH, JCI, ISO 45001).
- Improves infection control and clinical outcomes.
- Enhances patient trust and hospital reputation.
- Promotes a culture of safety and continuous improvement.
- RESIDENTIAL AND HIGH-RISE BUILDING SAFETY AUDIT: ENSURING RESIDENT WELL-BEING AND STRUCTURAL INTEGRITY
A residential and high-rise building safety audit is a thorough assessment aimed at identifying safety risks, ensuring compliance with regulations, and protecting residents from hazards. This audit covers structural safety, fire safety, electrical systems, emergency preparedness, and overall building security.
Objectives of a Residential and High-Rise Building Safety Audit
- Ensure compliance with local building and fire safety codes.
- Identify and mitigate risks to residents and visitors.
- Improve emergency response and evacuation preparedness.
- Enhance the safety and security of common areas.
- Promote sustainable and safe living conditions.
- HOTEL SAFETY AUDIT: ENSURING GUEST AND STAFF SAFETY
A hotel safety audit is a systematic assessment of hotel operations, facilities, and processes to identify potential risks and ensure the safety of guests, staff, and property. It covers fire safety, security, health and hygiene, emergency preparedness, and more, ensuring compliance with local regulations and international standards.
Benefits of a Hotel Safety Audit
- Protects guests, staff, and property from hazards.
- Ensures compliance with legal and regulatory requirements.
- Enhances hotel reputation and guest trust.
- Reduces liability risks and insurance premiums.
- Promotes a proactive safety culture.
- SCHOOL SAFETY AUDIT: CREATING A SAFE LEARNING ENVIRONMENT
A school safety audit is a thorough evaluation of a school’s physical environment, safety policies, and emergency procedures to ensure the well-being of students, staff, and visitors. It covers multiple aspects of safety, including physical security, health, emergency preparedness, and psychosocial factors.
Benefits of a School Safety Audit
- Reduces risks and protects students, staff, and visitors.
- Builds trust among parents and the community.
- Ensures compliance with regulatory standards.
- Creates a supportive environment for learning and development.
- Promotes a culture of safety and well-being.
- COMMERCIAL BUILDING SAFETY AUDIT: ENSURING WORKPLACE SAFETY AND REGULATORY COMPLIANCE
A commercial building safety audit is a comprehensive evaluation of a building’s infrastructure, operations, and safety systems to ensure the safety of occupants, assets, and visitors. It helps identify risks, ensure compliance with legal requirements, and promote a safe and efficient working environment.
Benefits of a Commercial Building Safety Audit
- Protects occupants and assets from risks.
- Ensures compliance with regulatory requirements.
- Reduces liabilities and insurance costs.
- Enhances operational efficiency and safety culture.
- Promotes a healthy and secure work environment.
- WORKING AT HEIGHTS SAFETY AUDIT: ENSURING SAFE PRACTICES AND COMPLIANCE
A Working at Heights Safety Audit assesses and verifies the safety measures, processes, and controls in place for workers operating at elevated levels. The audit ensures compliance with relevant safety standards and minimizes risks associated with working at heights. Falls from height remain one of the leading causes of workplace injuries and fatalities, making these audits essential for protecting workers and maintaining a safe environment.
Benefits of a Working at Heights Safety Audit
- Reduces workplace injuries and fatalities.
- Ensures compliance with safety regulations.
- Boosts worker confidence and productivity.
- Minimizes downtime and liability risks.
- Promotes a proactive safety culture
- CONSTRUCTION SAFETY AUDIT: ENSURING A SAFE AND COMPLIANT WORKSITE
A construction safety audit is a critical evaluation of a construction site to identify potential safety hazards, ensure compliance with legal and industry standards, and protect workers from risks. It focuses on assessing site conditions, equipment, processes, and overall safety management practices.
Benefits of a Construction Safety Audit
- Reduces accidents, injuries, and fatalities.
- Improves worker morale and productivity.
- Ensures compliance with regulations and standards.
- Minimizes project delays and liability risks.
- Enhances the overall safety culture on-site.
- SCAFFOLDING SAFETY: KEY GUIDELINES FOR A SAFE WORK ENVIRONMENT
Scaffolding safety is critical on construction sites to protect workers from falls, injuries, and potential fatalities. Proper planning, setup, and regular inspection of scaffolding systems are essential to prevent accidents. Scaffolding hazards mainly include falls, collapsing structures, and falling objects.
Scaffolding Safety Benefits
- Reduces the risk of accidents and injuries.
- Ensures compliance with legal and safety standards.
- Improves worker confidence and productivity.
- Minimizes project delays and associated costs.
- BEHAVIOR-BASED SAFETY (BBS) AUDIT
A BBS Audit evaluates the implementation, effectiveness, and sustainability of a Behavior-Based Safety program. It focuses on verifying that observations, feedback processes, and data-driven improvements are conducted effectively and aligned with the organization’s safety goals.
Benefits of BBS Audits
- Ensures the integrity and effectiveness of the BBS program
- Identifies behavioral trends and risk areas
- Improves employee engagement and trust in the process
- Promotes data-driven decision-making
- Supports continuous improvement and long-term safety performance
- PSYCHOLOGICAL ASSESSMENTS IN WORKPLACE SAFETY
Psychological assessments are tools used to evaluate an individual’s mental health, cognitive abilities, personality traits, emotional resilience, and stress response—critical factors that influence workplace safety and performance. These assessments help identify risks related to human behavior and mental well-being, contributing to proactive safety management.
Key Objectives of Psychological Assessments
- Assess mental readiness and emotional stability for high-risk tasks
- Identify cognitive and behavioral patterns that may lead to unsafe behaviors
- Evaluate stress management and resilience in crisis situations
- Support employee well-being and mental health initiatives
- Enhance safety culture by addressing psychological factors
- CONTRACTOR SAFETY MANAGEMENT (CSM)
Contractor Safety Management is a structured process to ensure that contractors and subcontractors meet an organization’s health, safety, and environmental (HSE) standards. Since contractors often perform high-risk tasks, managing their safety is critical to reducing workplace incidents and ensuring compliance with legal and regulatory requirements.
Objectives of Contractor Safety Management
- Ensure contractors comply with safety standards and legal requirements.
- Reduce workplace incidents and risks associated with contractor activities.
- Align contractor safety practices with the organization’s safety culture.
- Enhance monitoring, evaluation, and continuous improvement of contractor performance.
Key Steps in Contractor Safety Management
- Pre-Qualification and Selection
- Evaluate contractors’ safety performance history and competency.
- Require documentation of safety programs, training records, and certifications.
- Use a contractor pre-qualification questionnaire (focus on accident history, regulatory compliance, and HSE policies).
- Contractor Induction and Training
- Provide safety induction before starting work.
- Cover site-specific hazards, emergency procedures, PPE requirements, and safe work practices.
- Ensure job-specific training for high-risk tasks (e.g., working at heights, confined spaces).
- Risk Assessment and Safe Work Planning
- Conduct joint risk assessments with contractors.
- Develop Job Hazard Analysis (JHA) or Safe Work Method Statements (SWMS) for high-risk activities.
- Ensure control measures are in place for identified hazards.
- Monitoring and Supervision
- Assign safety supervisors to oversee contractor activities.
- Conduct regular site inspections and audits to ensure compliance.
- Use observation checklists to track adherence to safety procedures.
- Incident Reporting and Investigation
- Require contractors to report incidents and near-misses immediately.
- Conduct joint incident investigations to identify root causes and corrective actions.
- Share lessons learned with all contractors to prevent recurrence.
- Performance Evaluation and Continuous Improvement
- Track contractor safety performance with KPIs (e.g., total recordable incident rate, lost time injury frequency rate).
- Conduct regular performance reviews and feedback sessions.
- Reward contractors with strong safety records and improvement initiatives.
Benefits of Contractor Safety Management
- Improves Overall Safety Performance: Reduces risks from third-party activities.
- Ensures Regulatory Compliance: Meets legal and industry standards.
- Protects Business Reputation: Minimizes the risk of incidents involving external personnel.
- Enhances Collaboration: Encourages contractors to adopt a proactive safety approach.
Contractor Safety Audit
A Contractor Safety Audit is a structured evaluation to ensure contractors comply with the organization’s safety standards, legal regulations, and best practices. It focuses on identifying gaps, assessing risks, and improving contractor safety performance.
Objectives of a Contractor Safety Audit
- Verify contractor compliance with safety policies and procedures.
- Identify hazards and unsafe practices in contractor activities.
- Assess the effectiveness of contractor safety management systems.
- Ensure proper risk mitigation measures are in place.
- Drive continuous improvement in contractor safety performance.
Benefits of Implementing Contractor Safety Requirements
- Reduces workplace incidents and injuries.
- Ensures legal and regulatory compliance.
- Protects the organization’s reputation.
- Improves contractor productivity and performance.
- Fosters a positive safety culture across the organization.
- FIRE SAFETY AUDIT: ENSURING COMPREHENSIVE FIRE RISK MANAGEMENT
A Fire Safety Audit is a structured evaluation of fire hazards in a facility to ensure compliance with safety standards and reduce the risk of fire incidents. It focuses on identifying gaps in fire prevention, protection, and response measures, offering actionable recommendations to improve safety. Fire safety audits are essential for industries such as manufacturing, oil & gas, chemical plants, hospitals, schools, hotels, and high-rise buildings.
Key Benefits of Fire Safety Audit
- Early Risk Detection: Prevent potential fire incidents.
- Compliance: Ensure adherence to fire safety regulations.
- Enhanced Emergency Preparedness: Improve response times and minimize impact.
- Cost Savings: Reduce insurance premiums and prevent costly fire damage.
- Increased Employee Confidence: Create a safer working environment.
Who Needs a Fire Safety Audit?
- Manufacturing Plants
- Chemical and Petrochemical Facilities
- Warehouses and Storage Units
- Hospitals and Healthcare Centers
- Educational Institutions
- Commercial and Residential High-Rise Buildings
- Hotels and Hospitality Sector
Fire Audit: Comprehensive Fire Risk Assessment and Safety Compliance
A Fire Audit is a thorough evaluation of fire safety measures in a facility. It aims to assess fire hazards, ensure regulatory compliance, and improve fire prevention, protection, and emergency response systems. Fire audits are essential for safeguarding human lives, protecting assets, and minimizing business disruptions.
Benefits of a Fire Audit
- Early Detection of Hazards: Prevent fire incidents.
- Regulatory Compliance: Avoid penalties and legal issues.
- Improved Emergency Preparedness: Reduce response time and ensure safe evacuation.
- Enhanced Safety Culture: Increase fire safety awareness among employees.
- Cost Savings: Lower insurance premiums and avoid costly damages.
Industries Requiring Fire Audits
- Manufacturing and Processing Plants
- Oil & Gas Facilities
- Chemical Industries
- Warehouses and Logistics Centers
- Healthcare Institutions
- Educational Facilities
- Hospitality and High-Rise Buildings
4.ELECTRICAL SAFETY AND AUDIT: ENSURING RISK-FREE WORK ENVIRONMENTS
An electrical safety audit (ESA) is a comprehensive evaluation of an organization’s electrical systems and practices to identify hazards, ensure regulatory compliance, and promote safe working conditions. Electrical incidents can cause serious injuries, fires, equipment damage, and business disruptions, making these audits critical for workplace safety.
Common Hazards Found in Electrical Safety Audits
- Improper grounding and earthing systems.
- Overloaded circuits and use of unauthorized extensions.
- Poorly maintained or outdated electrical panels.
- Unprotected live parts and exposed wires.
- Lack of arc flash protection measures.
Benefits of Electrical Safety Audits
- Reduces electrical hazards and ensures a safer workplace.
- Prevents equipment failures and costly downtime.
- Ensures compliance with safety regulations.
- Improves energy efficiency and system reliability.
- Reduces insurance costs and liability risks.
Electrical Residual Life Assessment (RLA): Extending Equipment Lifespan and Ensuring Reliability
Electrical Residual Life Assessment (RLA) is a process used to determine the remaining useful life of electrical equipment and systems. This assessment helps identify aging-related issues, predict potential failures, and recommend actions for life extension or replacement. It is crucial for industries relying on continuous operations, such as power plants, manufacturing, oil & gas, and data centers.
Key Equipment Covered in Electrical RLA
- Transformers
- Motors and Generators
- Switchgears and Circuit Breakers
- Cables and Busbars
- Relays and Protection Systems
- Power Electronics (VFDs, UPS systems, etc.)
Benefits of Electrical Residual Life Assessment
- Failure Prevention: Identify potential failures before they occur.
- Cost Savings: Reduce unplanned maintenance and extend equipment life.
- Improved Reliability: Enhance system performance and reduce downtime.
- Optimized Capital Planning: Make informed decisions about equipment replacement and upgrades.
- Compliance: Meet regulatory and industry standards.
Thermography Assessments: Comprehensive Heat Mapping for Preventive Maintenance
A thermography assessment involves using infrared technology to detect temperature anomalies in electrical, mechanical, and structural systems. It’s an effective non-contact diagnostic method that provides insights into the condition of equipment, helping identify potential failures, reduce energy losses, and improve overall safety and reliability.
Applications of Thermography Assessments
- Electrical Systems
- Detect overheating in switchboards, circuit breakers, and control panels.
- Identify loose connections, overloaded circuits, and imbalanced loads.
- Spot insulation failures in cables and transformers.
- Mechanical Systems
- Assess temperature patterns in bearings, motors, and rotating equipment.
- Detect misalignment, lubrication issues, and excessive friction.
- Monitor HVAC systems (compressors, pumps, fans).
- Structural Assessments
- Identify heat loss in building insulation.
- Detect moisture intrusion and water leaks in roofs and walls.
- Assess fire hazards in storage areas.
- Process Industries
- Monitor temperature-sensitive processes.
- Ensure uniform heating in kilns, furnaces, and reactors.
- Detect leaks in steam and hot water systems.
Key Benefits of Thermography Assessments
- Early Fault Detection: Avoid costly breakdowns and unplanned downtime.
- Increased Safety: Reduce risks of electrical fires, equipment failures, and overheating.
- Energy Savings: Improve energy efficiency by detecting heat losses.
- Non-Intrusive: No need for system shutdowns during assessments.
- Compliance Support: Meet safety, insurance, and regulatory requirements.
Arc Flash Assessments: Protecting Personnel from Electrical Hazards
An Arc Flash Assessment evaluates the potential risks of arc flash incidents in electrical systems and helps implement measures to protect workers from severe injuries caused by these high-energy events. This assessment is critical for industries where electrical work is part of daily operations, such as manufacturing, power plants, oil & gas, and commercial buildings.
What is an Arc Flash?
An arc flash is an electrical explosion caused by a fault or short circuit in energized electrical equipment. It results in:
- Extreme heat (up to 35,000°F or 19,400°C)
- Blast pressure causing equipment damage and serious injury
- Molten metal and shrapnel ejected at high speed
- Intense light and sound
Key Benefits of Arc Flash Assessments
- Enhanced Worker Safety: Reduce the risk of serious injuries and fatalities.
- Compliance: Ensure adherence to safety standards and regulatory requirements.
- Improved Equipment Reliability: Minimize equipment damage and operational disruptions.
- Informed Decision-Making: Optimize maintenance and capital planning.
- Reduced Insurance Costs and Liability Risks.
- INDUSTRIAL HYGIENE AUDIT: SAFEGUARDING HEALTH IN THE WORKPLACE
An industrial hygiene audit is a comprehensive assessment of workplace environments to identify, evaluate, and control hazards that could affect employees’ health. It focuses on anticipating, recognizing, evaluating, and controlling occupational health risks related to physical, chemical, biological, and ergonomic factors.
Benefits of an Industrial Hygiene Audit
- Reduces health risks and prevents occupational illnesses.
- Enhances regulatory compliance and avoids penalties.
- Improves employee health, morale, and productivity.
- Reduces absenteeism and healthcare costs.
- Supports a proactive approach to workplace health management.
6) SAFETY CULTURE TRANSFORMATION
Safety Culture Transformation Process
A strong safety culture is essential for reducing incidents, improving operational efficiency, and achieving long-term success. Transforming safety culture requires a structured approach that involves leadership commitment, employee engagement, continuous learning, and behavioral changes.
- Assessment and Diagnosis
The transformation begins with a comprehensive assessment of the current safety culture.
- Leadership Commitment and Vision
Leadership plays a critical role in driving cultural change. Leaders must actively promote safety as a core organizational value.
- Building Engagement and Ownership
Employees should be involved in safety improvements and empowered to take ownership.
- Training and Competence Development
Transforming safety culture requires ongoing education and skill-building.
- Integrating Safety into Business Processes
Safety should be an integral part of operational and decision-making processes.
- Reinforcing Desired Behaviours
Encourage continuous improvement by reinforcing safe behaviors and addressing unsafe ones.
- Continuous Improvement and Sustainability
A safety culture transformation is a long-term process that requires sustained effort.
Safety Culture Maturity Stages
Organizations typically progress through these stages:
- Pathological – Safety is ignored or seen as a burden.
- Reactive – Safety improvements occur only after incidents.
- Calculative – Systems and processes are in place but not deeply embedded.
- Proactive – Safety is actively managed and continuously improved.
- Generative – Safety is a core value, and everyone takes responsibility for it.
Challenges in Safety Culture Transformation
- Resistance to change and complacency
- Lack of leadership commitment
- Inadequate communication and training
- Insufficient resources for safety initiatives
- Failure to measure and monitor cultural change
Success Factors
- Strong leadership and visible commitment
- Employee engagement at all levels
- Effective communication and feedback loops
- Integration of safety into core business processes
- Continuous improvement through monitoring and adaptation
Safety Perception Survey (SPS)
A Safety Perception Survey is a tool designed to gauge employees’ perceptions, attitudes, and beliefs regarding the safety culture within an organization. It helps identify gaps between management’s intentions and employees’ actual experiences related to workplace safety.
Why Conduct a Safety Perception Survey?
- Assess the current state of the safety culture
- Identify strengths and areas for improvement
- Promote employee engagement in safety initiatives
- Provide a baseline for measuring progress over time
- Benchmark results against industry standards
Behavior-Based Safety (BBS) is a proactive process that focuses on identifying and modifying unsafe behaviors in the workplace to prevent incidents and injuries. It emphasizes observing employees’ behavior, providing constructive feedback, and reinforcing safe practices.
Core Principles of BBS
- Focus on Behavior: Human behavior is the leading cause of workplace incidents.
- Employee Involvement: Employees are key in observing and correcting behavior.
- Positive Reinforcement: Encourage safe behavior rather than punishing unsafe practices.
- Data-Driven Process: Use observation data to identify trends and improve safety programs.
- Continuous Improvement: Regular feedback and reviews help sustain long-term change.
Benefits of Behavior-Based Safety
- Reduced Incidents and Injuries: Focuses on preventing at-risk behaviors.
- Improved Safety Culture: Encourages openness and shared responsibility.
- Higher Employee Engagement: Involves employees in safety processes.
- Data-Driven Decisions: Provides actionable insights from observation data.
- Sustained Long-Term Improvement: Encourages continuous growth and learning.
Safety Performance Leadership Survey
A Safety Performance Leadership Survey assesses how leadership attitudes, actions, and behaviors influence the organization’s safety culture and performance. This survey helps identify gaps, set improvement goals, and engage leadership in driving a safer workplace.
Purpose of the Survey
- Evaluate leaders’ commitment to safety.
- Measure perceptions of leadership’s influence on safety performance.
- Identify areas for improvement in safety leadership practices.
- Enhance accountability and engagement at all leadership levels.
Change Management in Safety and Organizational Processes
Change management is a structured approach to transitioning individuals, teams, and organizations from a current state to a desired future state. In safety and operational environments, managing change effectively ensures that safety risks are minimized, employees are engaged, and improvements are sustainable.
Objectives of Change Management
- Ensure the safety and well-being of employees during transitions.
- Minimize resistance and disruptions.
- Engage stakeholders to drive successful implementation.
- Identify and mitigate risks associated with changes.
- Build a resilient and adaptable organizational culture.
Types of Change in Safety and Operations
- Organizational Change – Restructuring, mergers, or leadership transitions.
- Process Change – New procedures, production methods, or standards.
- Technological Change – Implementation of new equipment or systems.
- Regulatory Change – Compliance with updated legal and safety standards.
- Cultural Change – Building a stronger safety culture or behavioral transformation.
Common Challenges in Change Management
- Resistance to Change: Fear of the unknown or loss of control.
- Poor Communication: Lack of clarity can lead to confusion and frustration.
- Insufficient Resources: Inadequate training, time, or tools can hinder success.
- Leadership Misalignment: Inconsistent leadership behaviors can undermine the process.
- Cultural Barriers: Deep-rooted organizational norms may resist change.
- SAFETY PROFESSIONALS PLACEMENT SERVICES
Safety professionals play a critical role in ensuring workplace safety, compliance, and risk mitigation. Many organizations rely on safety professionals placement services to recruit qualified safety officers, managers, and consultants who can help maintain regulatory compliance and create a safe work environment. However, the recruitment and placement of safety professionals come with unique challenges.
Safety professional’s placement services specialize in sourcing and hiring qualified experts for various industries, including:
- Construction & Engineering (Safety Officers, Site Safety Managers)
- Manufacturing & Industrial (Health & Safety Managers, Compliance Auditors)
- Oil & Gas, Energy, and Utilities (HSE Advisors, Risk Analysts)
- Healthcare & Pharmaceuticals (Infection Control Officers, Biosafety Experts)
- Supply Chain & Logistics (Transportation Safety Managers, Compliance Coordinators)
- Cybersecurity & Information Safety (Virtual CISOs, Security Compliance Experts)
Types of Placement Services
- Permanent Staffing – Recruiting full-time, long-term safety professionals.
- Contract & Temporary Staffing – Providing short-term or project-based professionals.
- Consulting & Advisory Services – Deploying experts to assess, audit, and develop safety programs.
- Virtual Safety Officers – Remote safety professionals who provide guidance and compliance monitoring.
- ISO 45001:2018-OCCUPATIONAL HEALTH AND SAFETY MANAGEMENT SYSTEM
Would you like Reduction of workplace incidents, reduced absenteeism and staff turnover, leading to increased productivity, reduced cost of insurance premiums, creation of a health and safety culture, whereby employees are encouraged to take an active role in their own OH&S, Reinforced leadership commitment to proactively improve OH&S performance, Ability to meet legal and regulatory requirements, Enhanced reputation and Improved staff morale.
ISO 45001:2018-OCCUPATIONAL HEALTH AND SAFETY MANAGEMENT SYSTEM. |
Health and safety in the workplace are the number one concern of most businesses, yet still deaths and injuries occur. ISO 45001 sets the minimum standard of practice to protect employees worldwide.
According to the International Labour Organization (ILO), there are currently more than 2.78 million deaths a year as a result of occupational accidents or work-related diseases, in addition to 374 million non-fatal injuries and illnesses. Aside from the enormous impact on families and communities, the cost to business and economies is significant.
1.What is ISO 45001?
ISO 45001, Occupational health and safety management systems – Requirements with guidance for use, is the world’s first International Standard for occupational health and safety (OH&S). It provides a framework to increase safety, reduce workplace risks and enhance health and well-being at work, enabling an organization to proactively improve its OH&S performance.
2.Why Implement ISO 45001?
- Makes a safe place to work.
- reduced number of incidents,
- employee absenteeism,
- employee turnover,
- reduced downtime and reductions in insurance premiums.
3.Applicable to:
Manufacturing such as Pharmaceuticals, Chemicals, Hospitals, Steel, Cement, Construction, Glass, Bakery, Paper and service industry like IT, ITeS.
- ism,
- employee turnover,
- reduced downtime and reductions in insurance premiums.
3.Applicable to: